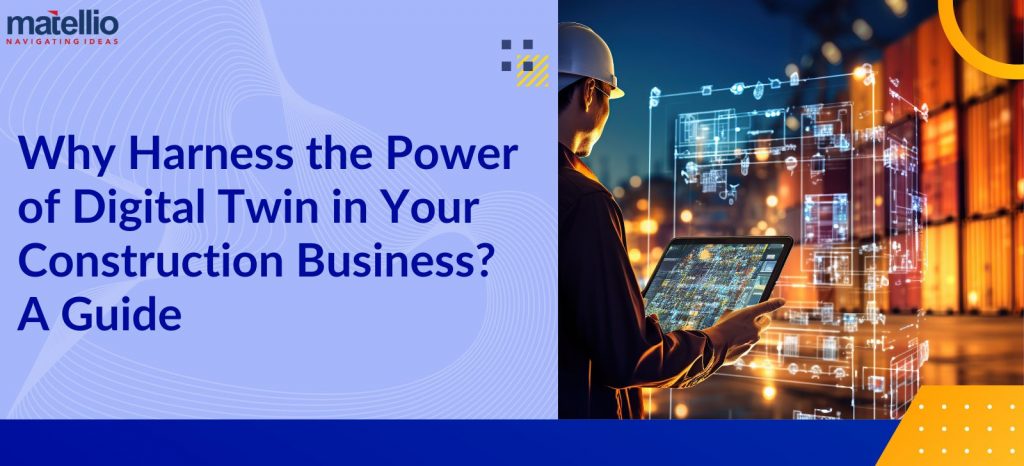
What if you could virtually simulate and analyze scenarios before physically executing your construction project? Well, that’s the basic idea around which digital twin in construction revolves.
According to a report, 55% of software technology decision-makers worldwide are currently embracing digital twins, employing them across various stages from design to maintenance. A digital twin refers to a virtual portrayal of a physical entity, individual, or operation set within a digital environment mirroring its real-world context. The technology allows businesses to simulate authentic scenarios and their potential consequences, thereby facilitating informed decision-making processes.
While that’s just a common definition, digital twin in construction has a much wider and dynamic scope. That’s why its implementation after seeking digital transformation services is becoming key to the AEC industry. It’s a multifaceted sector that involves diverse participants such as architects, engineers, contractors, property owners, and local authorities. The technology is versatile enough to let you optimize several operations in the construction industry. How? That’s what we’re going to unravel in this blog. So, without any further ado, let’s dive in!
What is Digital Twin in Construction?
A construction digital twin offers—a detailed virtual representation of your project. It’s not just a static image; it’s an interactive model that provides a wealth of information about the project’s structural intricacies, material characteristics, and environmental factors.
Through advanced technologies like 3D modeling and augmented reality, stakeholders can explore and interact with the digital twin, gaining valuable insights and making informed decisions. But it doesn’t stop there. Digital twin technology evolves alongside physical construction, allowing for preemptive issue detection, design optimization, and improved decision-making processes.
If we talk about how it functions, a digital twin in construction involves gathering real-world data using various technologies such as 3D laser scanners, drones, sensors, and cameras. This data is then combined and processed to build a detailed virtual representation of the physical structure. With the support of an AI or IoT development company, you can seek a digital twin that continuously learns and updates itself to reflect changes in the real-world counterpart.
So, when you harness digital twins in construction projects, your operations become more efficient, cost-effective, and sustainable. And the best part? You can access digital twins for your construction project through specialized software for the best results. Such a solution would serve as centralized hubs for storing, accessing, and sharing digital twin data, providing project stakeholders with a single source of truth.
Transform Your Construction Project Today with Digital Twin.
Benefits of Digital Twin in Construction
Your decision to seek customized solutions can enable you to gain digital twins that are precisely designed to match your construction team’s or project’s distinct needs. A tailored approach to construction management software development can keep you rest assured that the technology delivers optimal advantages and yields substantial value for your construction business. Some of the prominent benefits of the digital twin in construction sought through a specialized software are-
Enhanced Data Transparency and Availability
Ever felt like crucial construction data gets lost in a maze of different software systems and stakeholders? Digital twins are here to change that. Think of them as your construction project’s best friend, gathering all the essential data and putting it in one easy-to-access place. No more hunting for info across various platforms—digital twins streamline everything, making collaboration a breeze.
Real-time Monitoring and Analysis
Want to see exactly what’s happening on your construction site at any given moment? That’s what digital twins offer! Developed by a reliable IoT and AI development company, the technology can help you get instant insights into everything from resource usage to project progress. It’s like having a watchful eye on your project, ensuring everything stays on track.
Improved Collaboration
Collaboration is the name of the game in construction, but it can be tricky with so many players involved. Digital twins in construction are like the ultimate team players, bringing everyone together on one unified platform. No more misunderstandings or crossed wires; with digital twins, everyone’s on the same page, working towards a common goal.
Ability to Test What-If Scenarios
Ever wish you could peek into the future and see how different decisions might play out? Digital twins allow you to do that as well. They’re like a virtual playground where you can test out different scenarios and see the consequences before making any real-world changes.
Enabled Preventive Measures
Safety first, right? Digital twins in construction can take your safety and security game to a whole new level. They’re like your personal safety net, constantly scanning for potential risks and alerting you before disaster strikes. It’s like having a guardian angel watching over your construction site, ensuring everyone stays safe and sound.
Increased Accuracy
Precision is key in construction, and digital twins are masters of accuracy. They’re like your trusty GPS, guiding you through the construction process with pinpoint precision. No more guesswork or crossed fingers—digital twins ensure everything is spot-on, from planning to execution.
Digital Twin Use Cases in Construction
The use of digital twins in the construction industry has really changed the sector’s project initiation and completion. They totally amp up the analytical powers of building information modeling (BIM). It’s like taking your regular BIM model and giving it a high-tech makeover. With digital twin technology, stakeholders can see what’s happening in real time on the construction site, including the status, conditions, and exact positions of all the physical assets.
What’s more? Thanks to digital twins, facility owners and managers can basically clone every detail of their building into a digital world. It’s like having a virtual version of your actual structure, complete with all the measurements and data. And here’s the kicker—project teams can use these digital twins to run virtual experiments and predict how changes will play out before they even lift a hammer. The key applications, which are the reasons why construction teams are able to do so, are as follows-
- Design Visualization: Digital twins bring designs to life, offering detailed visualizations of projects before any physical work begins.
- Clash Detection: Early identification of potential clashes between structural elements, systems, or equipment is made possible by digital twins, saving time and resources.
- Construction Planning and Sequencing: Precise planning of construction activities is achievable through digital twins, optimizing workflows and minimizing delays by effectively sequencing tasks.
- Safety Planning and Training: Virtual safety simulations enable comprehensive safety planning and personnel training in a risk-free environment, ensuring workforce safety.
- Progress Monitoring and Reporting: Real-time monitoring and reporting of project progress are facilitated by digital twins, keeping teams informed about milestones and potential deviations from the plan.
- Predictive Maintenance: Equipment failures can be predicted and prevented with digital twins analyzing sensor data, reducing downtime, and extending equipment lifespan.
- Energy Efficiency Analysis: Optimizing energy usage and suggesting efficiency improvements from the outset is made possible by digital twins simulating various scenarios.
- Facility Management: Throughout its lifecycle, efficient facility management is supported by digital twins, offering insights for maintenance, space utilization, and overall performance optimization.
- Retrofitting and Renovation: Confident planning of renovations and retrofits is facilitated by digital twins, ensuring compatibility and minimizing disruption through simulated changes.
- Lifecycle Performance Analysis: Continuous improvement is supported by digital twins tracking performance data over time, providing valuable feedback from past projects.
Also Read- Digital Twin Software: Transforming Industries with Advanced Virtual Modeling
Digital Twin Examples in Construction
Several notable architecture and construction companies have embraced digital twins, revolutionizing their project methodologies. Below are a few examples from top construction firms illustrating how they harnessed the advantages of digital twins to enhance their processes. Remember, you can initiate similar projects starting with technology consulting services.
Morandi Bridge in Italian Genoa
Italferr S.p.A, a division of the Italian State Railways Group, used BIM models and digital twin workflows to expedite the reconstruction of the Morandi Bridge, a critical link between Italy and France’s road systems. The digital twin technology enabled them to ensure precise designs, fostered seamless collaboration among diverse project teams, and maintained a centralized source of truth.
LAX Reconstruction
During the reconstruction of Los Angeles International Airport (LAX), architecture and design firm Corgan leveraged digital twin technology to optimize performance. With this implementation, they accurately captured existing building conditions and facilitated efficient collaboration throughout the reconstruction process. Moreover, Corgan shared the 3D digital twin with facility owners, empowering advanced facility management capabilities.
Smart Cities Development
Digital twins in the construction industry are also becoming popular for smart cities. The technology is establishing replicas for numerous metropolitan areas and even small towns. These city-scale digital twins hold immense value, enabling more sustainable and eco-friendly construction practices, reducing carbon footprints, optimizing traffic flow, and monitoring infrastructure assets. Ultimately, comprehensive city digital twins have the potential to enhance residents’ quality of life and foster environmentally conscious urban spaces.
Elevate Your Construction Business with Custom Digital Twin Solutions.
Challenges of Implementing Digital Twin in Construction
When diving into the realm of digital twins for construction, it’s not just about hopping on the tech bandwagon; it’s about navigating a landscape filled with hurdles. Let’s break down some of these challenges.
Contractual Confusion
Contracts in construction can be as thick as a brick. Integrating digital twins means you can decipher how they fit into these legal labyrinths. Detailed records and clear communication are key to ensuring everyone on your team is on the same contractual page.
Data Dilemma
Construction firms often find themselves drowning in a sea of data. From disparate systems to real-time access struggles, making sense of it all might feel like finding a needle in a haystack.
BIM Bump
While some are stuck in the 2D past, transitioning to Building Information Modeling (BIM) requires a quantum leap. It’s like going from a chalkboard to a virtual reality headset. New tools and skill sets are essential for navigating this brave new world.
Structural Snags
Without solid processes for data exchange and issue resolution, introducing digital twins in construction can feel like building a house of cards in a hurricane. But once established, they become the bedrock that keeps everyone in sync.
Tech Trepidation
Embracing digital twins means confronting tech phobias head-on. From old-school skeptics to tech novices, getting everyone on board can feel like a hectic task.
Budget Barriers
Let’s face it: innovation often comes with a hefty price tag. Businesses must weigh the cost of implementing digital twins in construction against the potential benefits. It’s a delicate balancing act between investment and return on investment.
How Does Matellio Help Overcome the Challenges of Implementing Digital Twin in Construction?
Whether it’s deciphering complex contracts, wrangling mountains of data, or making the leap to BIM, Matellio has the tools and expertise to smooth out the bumps in the road. Our software development process can help you with seamless digital twin integration in your construction projects!
Understanding Your Vision
We start by sitting down with you to understand your vision for leveraging digital twins in construction. Whether it’s improving project coordination, enhancing communication, or optimizing asset management, we want to get a clear picture of your goals.
Site Assessment
Next, we conduct a thorough assessment of your construction site(s). Site assessment involves gathering data on existing infrastructure, layouts, and any relevant assets that will be part of the digital twin.
Data Collection and Integration
With the site assessment complete, we move on to data collection. This can include architectural drawings, engineering plans, sensor data, and more. We then integrate this data into the digital twin platform, ensuring it’s accurate and up-to-date.
Modeling and Simulation
Using advanced modeling techniques, we create a digital replica of your construction site. This includes 3D models of buildings, structures, and other elements. We can also simulate various scenarios to test different construction methods or identify potential issues before they arise.
IoT Integration
To make your digital twin truly interactive, we integrate IoT sensors throughout the construction site. You can seek our IoT integration services to employ sensors that monitor everything from temperature and humidity to equipment usage and worker movements, providing real-time data that enhances decision-making.
Visualization and Interface Design
We design a user-friendly interface that allows you to interact with your digital twin easily. This could be a web-based dashboard, mobile app, or augmented reality (AR) experience, depending on your preferences and needs.
Testing and Optimization
Before deployment, we rigorously test the digital twin in a construction project to ensure it performs flawlessly. We look for any bugs or glitches and optimize the platform for maximum efficiency and reliability.
Deployment and Training
Once testing is complete, we deploy the digital twin on-site and provide training to your team on how to use it effectively. We want to ensure everyone feels comfortable navigating the platform and understands its capabilities.
Continuous Monitoring and Updates
Our job doesn’t end once the digital twin is live. We provide ongoing support and monitoring to ensure everything runs smoothly. We also incorporate feedback from users and make updates to the platform as needed to keep it relevant and useful.
Also Read- How to Develop a Successful Construction Management Software?
Consult Experts to Integrate Digital Twin in Your Construction Business.
The Bottom Line
Matellio understands that digital twins are expected to continue to transform the construction industry. Therefore, the projects we take up for this technology’s implementation are executed by our experts with rigorous attention to detail and a commitment to excellence. Thus, if you are planning to implement digital twins in your next construction or engineering project, know that we’ve got the team, tech stack, and experience to deliver next-gen tech solutions successfully. Get started by filling out the form and embark on your journey towards innovation today!
Frequently Asked Questions (FAQs)
What is a digital twin in BIM?
A digital twin in BIM is a virtual replica of a physical building or structure. It integrates real-time data to simulate the behavior and performance of the asset throughout its lifecycle, aiding in the design, construction, and operation phases.
What type of software is used for digital twins?
Digital twins typically use specialized software platforms. Such systems offer centralized storage and sharing of digital twin data, providing stakeholders with a unified source of truth.
What is digital twin in structural engineering?
In structural engineering, a digital twin is a virtual representation of a physical structure. It incorporates real-time data to simulate structural behavior, enabling engineers to analyze performance, detect issues, and optimize designs before construction begins.
What are digital twins in civil infrastructure systems?
Digital twins in civil infrastructure systems are virtual replicas of physical infrastructure assets such as roads, bridges, and utilities. They leverage real-time data to monitor and analyze asset performance, optimize maintenance schedules, and enhance overall system efficiency.
What is the use of digital twins in architecture?
Digital twins in architecture enable architects to visualize and simulate building designs in a virtual environment. They help assess design feasibility, analyze spatial relationships, and optimize building performance before construction starts, leading to more efficient and sustainable architectural solutions.