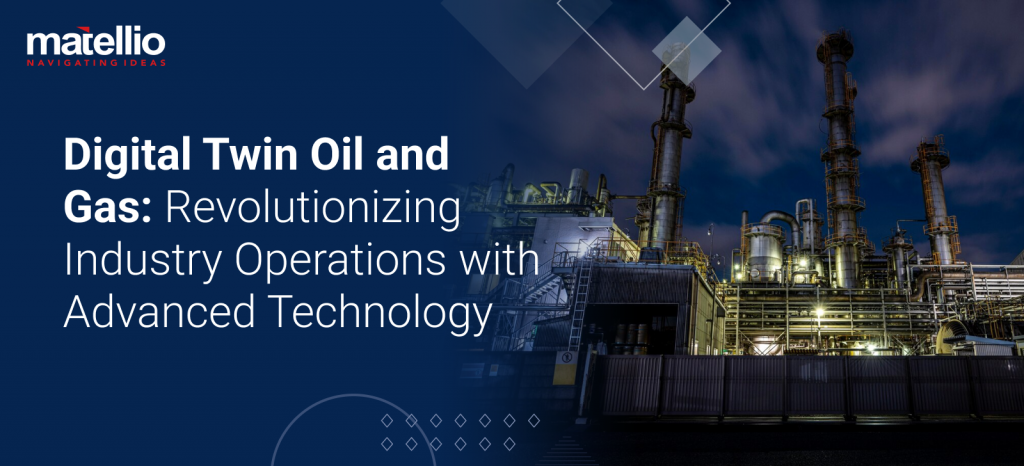
Introduction
In the oil and gas sector, digital twin technology is not just a trend; it’s a strategic investment driving substantial advancements in operational efficiency and decision-making. This technology creates dynamic, virtual representations of physical assets, integrating real-time data and predictive analytics to simulate operations and forecast future performance.
Digital twin technology in oil and gas facilitates predictive maintenance, optimizes drilling and reservoir management, and enhances safety and emergency preparedness. For instance, it allows operators to simulate various scenarios, optimize operations, and improve decision-making processes. Furthermore, as the industry embraces digitalization, the role of digital twins is set to expand, integrating with AI, machine learning, and IoT to offer even more sophisticated capabilities.
As we delve deeper into the transformative potential of digital twins in the oil and gas industry, we will explore how this technology improves current operations and lays the groundwork for future innovation and sustainability.
Understanding Digital Twin Technology in the Oil and Gas Industry
Digital twin technology, a pivotal innovation in the oil and gas sector, offers a sophisticated virtual model that mirrors physical assets. This model integrates historical data, real-time operational data, and predictive analytics to forecast the performance of oil and gas operations. At its core, a digital twin is a dynamic, virtual representation, simulating the behavior of oil and gas assets and processes to facilitate informed decision-making and strategic planning.
Key Components of Digital Twin Technology
Data Integration and Analysis
Digital twin technology amalgamates data from various sources, including sensors, operational records, and 3D models, to comprehensively view the asset’s performance and potential issues.
Predictive Maintenance
By continuously analyzing data, digital twins predict equipment failures, enabling preemptive maintenance and reducing downtime, a crucial benefit for the oil and gas industry, where equipment failure can result in significant financial losses and safety hazards.
Operational Efficiency
Digital twins simulate different operational scenarios to optimize processes. For instance, they can identify the most efficient ways to extract resources, reduce energy consumption, and minimize environmental impact.
Safety and Risk Management
Enhancing safety protocols, digital twins simulate potential hazardous scenarios, allowing companies to develop and test safety measures in a risk-free environment.
The Impact on the Oil and Gas Sector
Digital twin technology in oil and gas is a futuristic concept and a present reality reshaping the industry. It enables companies to enhance operational efficiency, reduce costs, and improve safety standards. With the ability to simulate and analyze operations in real time, companies can make proactive decisions that significantly impact their productivity and sustainability.
For instance, predictive maintenance facilitated by digital twins can prevent costly unplanned outages, while optimization of drilling and extraction processes ensures that resources are used efficiently, thereby increasing profitability. Embracing digital transformation services is crucial for oil and gas companies aiming to integrate digital twin technology effectively, ensuring a seamless transition into this innovative operational paradigm.
Experience the Future of Oil and Gas with Advanced Digital Twin Technology.
The Role of Digital Twin in the Oil and Gas Industry
Digital twin technology is revolutionizing the oil and gas industry by providing a powerful tool for monitoring, analyzing, and optimizing the performance of assets across the entire value chain. Leveraging technology consulting services can give oil and gas businesses the expertise needed to maximize digital twin technology, enhancing operational efficiency and strategic decision-making. This section delves into the multifaceted role of digital twin technology in the oil and gas industry, underscoring its potential to transform traditional operations into intelligent, data-driven processes.
Enhancing Operational Visibility and Control
Digital twin technology offers a comprehensive view of oil and gas operations, from upstream exploration and production to downstream refining and distribution. Digital twins provide real-time insights into their condition and performance by creating virtual replicas of physical assets. This visibility allows for better control over operations, facilitating swift and informed decision-making that can lead to significant efficiency gains.
Predictive Maintenance and Downtime Reduction
One of the most impactful applications of digital twin for oil and gas is predictive maintenance. By analyzing data from various sensors and historical performance records, digital twins can predict potential equipment failures before they occur. This proactive approach to maintenance can substantially reduce unplanned downtime, minimize repair costs, and extend the lifespan of critical assets, thereby enhancing overall operational efficiency.
Also Read- How to Develop IoT Predictive Maintenance Solution?
Optimizing Asset Performance and Lifecycle
Digital twins enable oil and gas companies to maximize the value of their assets throughout their lifecycle. By simulating different operational scenarios and analyzing the potential impact of various factors, companies can optimize the performance of their assets, improve recovery rates, and ensure sustainable operations. This optimization can lead to more effective resource utilization and a better return on investment.
Supporting Safety and Compliance
Safety is paramount in the oil and gas sector, and digital twin technology is crucial in enhancing safety measures. By simulating various scenarios, including potential emergencies, companies can identify risks and develop strategies to mitigate them effectively. Moreover, digital twins can help ensure compliance with industry regulations and standards, reducing the risk of environmental incidents and legal issues.
Facilitating Innovation and Future Planning
Digital twin technology improves current operations and paves the way for innovation and future growth in the oil and gas industry. It allows companies to test new ideas and technologies in a virtual environment, reducing the risks and costs associated with physical trials. This capability supports strategic planning and investment decisions, ensuring companies remain competitive in a rapidly evolving industry landscape.
In conclusion, the digital twin for oil and gas is a game-changer, offering comprehensive benefits that extend from operational efficiency and cost savings to enhanced safety and strategic innovation. As we proceed, we will explore real-world examples to illustrate the practical application and benefits of digital twin technology in the oil and gas industry, further emphasizing its transformative impact.
Examples of Digital Twin Use Cases in the Oil and Gas Industry
Implementing digital twin use cases in the oil and gas industry has led to numerous success stories, showcasing its ability to transform operations, enhance efficiency, and improve decision-making processes. These examples highlight the industry’s practical applications and benefits of digital twins.
Case Study 1: Offshore Drilling Optimization
One notable example is the use of digital twins in offshore drilling operations. A leading oil and gas company employed digital twin technology to create a virtual model of its offshore drilling platform. This model integrated real-time data from various sources, including sensors and operational systems, to simulate drilling processes and predict the performance of the drilling equipment. By analyzing this data, the company could optimize drilling parameters, reduce the risk of equipment failure, and enhance overall operational efficiency. This proactive approach not only improved the safety and reliability of drilling operations but also resulted in significant cost savings and reduced environmental impact.
Case Study 2: Pipeline Integrity Management
Another example involves the use of digital twins for pipeline integrity management. A major oil and gas operator developed a digital twin of its extensive pipeline network to monitor the condition of the pipes and predict potential failures. The digital twin technology enabled the company to conduct virtual inspections and simulations, identifying areas at risk of leaks or ruptures. The company proactively addressed these risks through predictive analytics, ensuring the safe and efficient transport of oil and gas and minimizing the likelihood of environmental disasters.
Case Study 3: Reservoir Performance Optimization
In reservoir management, digital twins have been instrumental in optimizing performance and extending the life of oil and gas fields. For instance, a digital twin of an oil reservoir allowed a company to simulate different extraction scenarios, assess reservoir behavior under various conditions, and optimize extraction strategies. This led to enhanced recovery rates, maximized asset value, and prolonged reservoir lifespan, showcasing the digital twin’s capability to support sustainable and profitable operations.
These real-world examples of digital twin for oil and gas illustrate its profound impact on enhancing operational efficiency, reducing risks, and driving innovation. As companies continue to adopt and integrate digital twins into their operations, the industry’s potential for further transformation and improvement remains significant. Collaboration with a reputable IoT development company enables oil and gas operators to integrate advanced sensors and data analytics into their digital twin solutions, enriching the model’s accuracy and functionality.
Advanced Applications: Digital Twin for Oil and Gas
Digital twin technology is advancing rapidly in the oil and gas industry, enhancing existing operations and enabling innovations and efficiencies. These advancements are revolutionizing the sector, highlighting the potential of digital twin technology to drive significant change.
Integrated Asset Management
Digital twin technology enables more effective asset management, allowing companies to create comprehensive digital replicas of facilities or infrastructures. These replicas provide real-time monitoring and performance analysis, leading to optimized asset utilization, reduced maintenance costs, and improved operational efficiency. This holistic approach ensures that every asset component, from individual machinery to entire production lines, functions optimally, minimizing inefficiencies and preventing downtime.
Enhanced Exploration and Production
In exploration and production, digital twins can accurately simulate geological and reservoir conditions. Companies can model various scenarios to identify the most effective drilling locations and extraction methods, reducing risks and maximizing returns. This advanced application of digital twin technology improves the precision of exploration activities and the efficiency of extraction processes, ultimately enhancing the profitability of oil and gas operations.
Supply Chain and Logistics Optimization
Digital twin technology provides advanced solutions for optimizing supply chain and logistics in the oil and gas industry. By creating digital replicas of the supply chain, companies can gain insights into the flow of materials and products, enabling real-time tracking, predictive maintenance of transport equipment, and improved logistics planning. This leads to more efficient operations, reduced costs, and enhanced supply chain visibility, ensuring timely delivery of materials and products.
Sustainability and Environmental Management
Digital twins are pivotal in promoting sustainability and environmental management within the industry. They allow companies to simulate the operational impacts and ecological conditions, aiding in assessing and mitigating the environmental footprint. This supports the development of strategies to reduce emissions, manage waste, and comply with environmental regulations, aligning with global sustainability goals.
Real-time Performance Monitoring and Optimization
Advanced digital twin applications enable real-time performance monitoring and optimization of oil and gas operations. Incorporating AI development services into digital twin technology allows for more sophisticated predictive analytics and machine learning capabilities, driving innovation and efficiency in oil and gas operations. By continuously analyzing data from various sources, digital twins can optimize real-time performance, adjust operational parameters to enhance efficiency, and predict potential issues before they occur, facilitating preemptive action.
Collaborative Engineering and Design
Digital twins facilitate collaborative engineering and design, allowing teams to work together on the virtual model, regardless of their physical location. This collaboration leads to better design choices, faster project completion, and reduced costs, enabling engineers to test and refine processes in a virtual environment before implementation in the real world.
Advanced Training and Simulation
Digital twins offer advanced training and simulation opportunities for oil and gas industry personnel. By replicating real-world scenarios in a risk-free virtual environment, employees can gain valuable experience and training, enhancing their skills and preparedness for on-site operations.
These advanced applications of digital twin for oil and gas underscore its capacity to drive innovation, efficiency, and sustainability. As the industry continues to navigate its digital transformation journey, the strategic implementation of digital twins will be crucial in achieving operational excellence and environmental stewardship, shaping the future of the oil and gas sector.
Use Cases of Digital Twin Technology in the Oil and Gas Industry
Digital twin technology in the oil and gas industry encompasses a broad spectrum of use cases, each offering unique benefits and improvements to traditional operations. These digital twin use cases in the oil and gas industry illustrate the technology’s versatility and capacity to address various challenges within the sector.
Reservoir and Field Management
Digital twins significantly enhance reservoir and field management by providing detailed simulations and analyses of reservoir behavior. This use case allows companies to optimize recovery strategies, improve field development planning, and make more accurate predictions about production levels. Using digital twins, engineers can simulate different extraction methods and operational scenarios to determine the most effective strategies for maximizing reservoir performance and extending field life.
Asset Lifecycle Management
Another vital digital twin use case for oil and gas is in asset lifecycle management. Digital twins offer a comprehensive view of an asset’s life cycle, from design and construction to operation and decommissioning. This holistic approach enables companies to optimize the performance and maintenance of assets, reduce lifecycle costs, and enhance operational safety. Through continuous monitoring and analysis, digital twins help identify potential issues before they become significant problems, facilitating proactive maintenance and extending asset lifespan.
Drilling Optimization
Digital twins are revolutionizing drilling operations by allowing companies to simulate and analyze drilling processes in advance. This use case helps optimize drilling parameters, enhance well placement accuracy, and reduce the risks associated with drilling activities. With digital twin technology, companies can model different drilling scenarios, assess the impact of various drilling strategies, and choose the most efficient and effective approach, leading to improved productivity and reduced operational costs.
Safety and Emergency Response
Digital twins offer a game-changing approach to safety and emergency response. They enable companies to simulate emergency scenarios and evaluate the effectiveness of their response plans in a risk-free environment. This use case enhances preparedness for potential incidents and improves overall safety management. By analyzing the virtual responses to emergencies, companies can fine-tune their safety protocols, train personnel more effectively, and ensure a rapid and coordinated response in real-life situations.
Environmental Impact Assessment
Digital twins also facilitate assessing and managing environmental impacts in the oil and gas industry. By simulating operations and their environmental effects, companies can better understand and mitigate the ecological footprint of their activities. This use case supports the development of strategies for reducing emissions, managing waste, and ensuring compliance with environmental regulations, contributing to more sustainable operations.
These digital twin use cases in the oil and gas industry highlight its transformative potential and its diverse benefits. By leveraging digital twins, companies can enhance operational efficiency, improve decision-making, reduce risks, and promote sustainability. As we move forward, the continued evolution and integration of digital twin technology will undoubtedly shape the future of the oil and gas sector.
Optimize Your Operations with Our Expert Digital Twin Technology.
Integrating Digital Twin with Other Technologies in the Oil and Gas Industry
Digital twin technology in the oil and gas industry is not an isolated solution; its integration with other cutting-edge technologies like AI, IoT, and automation significantly enhances its capabilities and benefits. This synergy between digital twins and other technologies leads to a more comprehensive and efficient approach to managing oil and gas operations.
AI and Machine Learning
Integrating artificial intelligence (AI) and machine learning (ML) with digital twins creates powerful tools for predictive analytics and decision-making. AI algorithms analyze the vast amounts of data generated by digital twins, identifying patterns and predicting potential issues before they occur. This predictive capability enables proactive maintenance and operational adjustments, reducing downtime and optimizing performance.
IoT Connectivity
Internet of Things (IoT) technology plays a crucial role in the functionality of digital twins. IoT devices and sensors provide the real-time data that digital twins need to represent physical assets accurately. This continuous data stream ensures that the digital twin remains an up-to-date virtual model of its physical counterpart, allowing for real-time monitoring and control of oil and gas operations.
Automation and Robotics
Automation and robotics, when integrated with digital twin technology, significantly improve operational efficiency and safety. Digital twins can control and monitor automated processes and robotic systems, providing a virtual platform for testing and optimizing automated workflows. This integration is particularly beneficial in hazardous or inaccessible areas, where robots can perform tasks under the guidance of the digital twin, minimizing human exposure to risk.
Cloud Computing and Big Data
Cloud computing and big data analytics are also integral to the enhanced functionality of digital twins. The cloud offers a scalable and accessible platform for storing and processing the large volumes of data associated with digital twins. Big data analytics, on the other hand, provide the tools to analyze this data, uncovering insights that can lead to improved operational strategies and decision-making.
By integrating with these technologies, the digital twin for oil and gas becomes a more powerful and versatile tool. It improves the accuracy and efficiency of operational processes and provides a foundation for innovation and continuous improvement in the sector. The following sections will address the challenges faced in implementing digital twin technology and how companies can overcome these to realize the benefits of this transformative tool fully.
Challenges and Solutions in Implementing Digital Twin Technology in Oil and Gas
Implementing digital twin for oil and gas offers significant benefits but presents unique challenges. Understanding these challenges and identifying solutions is crucial for companies successfully leveraging digital twin technology.
Data Integration and Management
- Challenge: One of the primary challenges is the integration and management of data from diverse sources. The oil and gas industry relies on data from various sensors, systems, and operations, which must be harmonized and managed effectively to create an accurate and functional digital twin.
- Solution: Implementing robust data integration platforms and adopting standardized protocols can facilitate the seamless aggregation of data. Investing in advanced data management systems ensures the reliability and accessibility of the data needed for effective digital twin operations.
Cybersecurity and Data Privacy
- Challenge: With the increased connectivity and data integration comes the heightened risk of cybersecurity threats and data breaches. Protecting sensitive operational and financial data is paramount in the high-stakes environment of the oil and gas sector.
- Solution: Companies must prioritize cybersecurity by implementing state-of-the-art security measures, including encryption, access control, and regular security audits. Developing a comprehensive cybersecurity strategy that includes risk assessment and incident response plans is essential.
Technological Complexity and Workforce Adaptation
- Challenge: The complexity of digital twin technology and the need for a skilled workforce to manage and interpret digital twin data can be a significant hurdle. The gap in digital skills in the workforce can impede the effective use of digital twins.
- Solution: Ongoing training and development programs are crucial to equip the workforce with the necessary skills to manage digital twin technology. Partnering with technology providers for training and support can facilitate smoother implementation and adoption.
Cost and Investment
- Challenge: The initial investment required for setting up digital twin technology can be substantial, especially for small to medium-sized enterprises. The cost of advanced sensors, data storage, and analytics platforms can hinder adoption.
- Solution: Companies should approach digital twin technology as a long-term investment and explore cost-effective solutions such as cloud-based services, which can reduce upfront costs. Demonstrating the potential ROI through pilot projects can also help in securing investment.
Scalability and Flexibility
- Challenge: As the oil and gas operations expand, the digital twin system must be scalable and flexible enough to accommodate growth and changes in the operational environment.
- Solution: Designing digital twins with scalability in mind and using modular and adaptable frameworks can ensure that the technology grows with the company. Regular updates and upgrades to the digital twin platform can also maintain its relevance and effectiveness.
In conclusion, while challenges exist in implementing digital twin for oil and gas, strategic planning, investment in technology and training, and a focus on cybersecurity can enable companies to overcome these obstacles and fully harness the benefits of digital twins. The final section will explore the prospects of digital twin for oil and gas, highlighting the ongoing innovations and trends shaping this dynamic field.
Also Read- Automation in Oil and Gas: Powering Tomorrow’s Energy Solutions
The Future of Digital Twin in the Oil and Gas Industry
The future of digital twin for oil and gas is marked by continuous innovation and transformative potential. As companies increasingly recognize the value of digital twins, the technology is set to become more integrated, sophisticated, and essential to the sector’s operations.
Advanced Integration with Emerging Technologies
Integrating digital twins with emerging technologies like blockchain, advanced analytics, and augmented reality will enhance the oil and gas industry’s transparency, efficiency, and collaboration. For example, blockchain can secure the data flow within digital twins, ensuring tamper-proof records and trust in shared data. Combined with digital twins, augmented reality can provide immersive training and maintenance experiences, improving safety and operational performance.
Autonomous Operations
The progression towards fully autonomous operations is a significant trend shaping the future of digital twins in the oil and gas industry. Digital twins will be crucial in automating complex processes, from drilling to logistics, enabling more efficient, safe, and cost-effective operations. Simulating and monitoring operations in real time allow for quicker adjustments and decision-making, paving the way for self-optimizing systems.
Enhanced Decision-Making with AI and Big Data
The convergence of digital twins, AI, and big data analytics will lead to more sophisticated decision-making tools. AI algorithms will process the vast amounts of data generated by digital twins to provide predictive insights and proactive recommendations, further optimizing oil and gas operations and reducing risks.
Sustainability and Environmental Management
As the oil and gas industry continues to face environmental and sustainability challenges, digital twins will become pivotal in managing these aspects. By accurately simulating the environmental impact of operations, digital twins can help companies develop more sustainable practices, reduce emissions, and comply with environmental regulations.
Market Expansion and New Business Models
The continued evolution of digital twin technology will also open up new markets and opportunities for innovative business models in the oil and gas industry. Companies can leverage digital twins to offer as-a-service models, providing real-time operational insights and optimization strategies to smaller operators without needing large upfront investments.
In conclusion, the future of the digital twin for oil and gas is bright, with significant advancements that promise to revolutionize the sector further. As digital twins become more integrated with other technologies, they will continue to drive operational excellence, innovation, and sustainability in the oil and gas industry, ensuring its competitiveness and relevance in the digital age. Adopting comprehensive enterprise solutions that include digital twin technology will be instrumental for oil and gas companies striving to achieve operational excellence and sustainable growth in the digital era.
Lead the Industry with Cutting-Edge Digital Twin Solutions.
Conclusion: Embracing Digital Twin Technology in the Oil and Gas Sector
As we have explored, the digital twin for oil and gas represents a significant leap forward in operational efficiency, risk management, and strategic planning. By providing a comprehensive, real-time virtual model of physical assets and processes, digital twins offer unparalleled insights and predictive capabilities, driving smarter decisions and more effective operations.
Recap of Key Benefits
- Operational Efficiency: Digital twins enhance operational efficiency by enabling real-time monitoring and optimization of processes, leading to reduced downtime and cost savings.
- Risk Management: They improve safety and risk management by simulating potential hazards and enabling proactive measures to mitigate them.
- Strategic Planning: Digital twins facilitate informed decision-making and strategic planning, allowing companies to anticipate market changes and adapt their strategies accordingly.
- Sustainability: They support sustainability efforts by enabling companies to monitor and manage their environmental impact more effectively.
The Road Ahead
The journey of integrating digital twin for oil and gas is ongoing. As the technology evolves and integrates further with AI, IoT, and other emerging technologies, its potential will continue to expand. Companies in the oil and gas sector must remain agile, embracing these advancements to stay competitive and relevant in a rapidly changing industry landscape.
For oil and gas companies looking to thrive in the digital age, investing in digital twin technology is not just an option but a necessity. It’s time to leverage the power of digital twins to transform operations, enhance efficiency, and drive sustainable growth. Matellio, with its expertise in digital transformation services, stands ready to guide and support businesses in this journey, ensuring they fully realize the benefits of digital twin technology in their operations.
In conclusion, the digital twin for oil and gas is not just about keeping pace with digital transformation; it’s about setting the pace, leading the change, and shaping the sector’s future. As we move forward, the adoption and integration of digital twins will undoubtedly play a pivotal role in defining the trajectory of the oil and gas industry, heralding a new era of efficiency, sustainability, and innovation.
FAQs
What is Digital Twin Technology in Oil and Gas?
Digital twin technology in oil and gas refers to creating a digital replica of physical assets, processes, or systems, allowing companies to simulate, predict, and optimize operations through real-time data and analytics.
How Does Digital Twin Technology Benefit the Oil and Gas Industry?
Digital twin technology enhances operational efficiency, improves safety protocols, enables predictive maintenance, and supports decision-making processes, leading to cost savings and increased productivity in the oil and gas sector.
Can Digital Twin Technology Reduce Operational Risks in Oil and Gas?
Yes, digital twin technology can significantly reduce operational risks by providing detailed simulations and predictive analytics, which help identify potential issues and mitigate risks before they escalate.
What are Some Real-World Examples of Digital Twin in Oil and Gas?
Real-world examples include using digital twins to optimize drilling operations, manage pipeline integrity, and enhance reservoir performance, demonstrating the technology's impact on improving efficiency and reducing costs.
What Future Developments Are Expected in Digital Twin Technology for Oil and Gas?
Future developments include the integration of AI and machine learning for advanced predictive analytics, wider adoption of IoT for real-time data collection, and increased use of digital twins in sustainability efforts to minimize environmental impact.