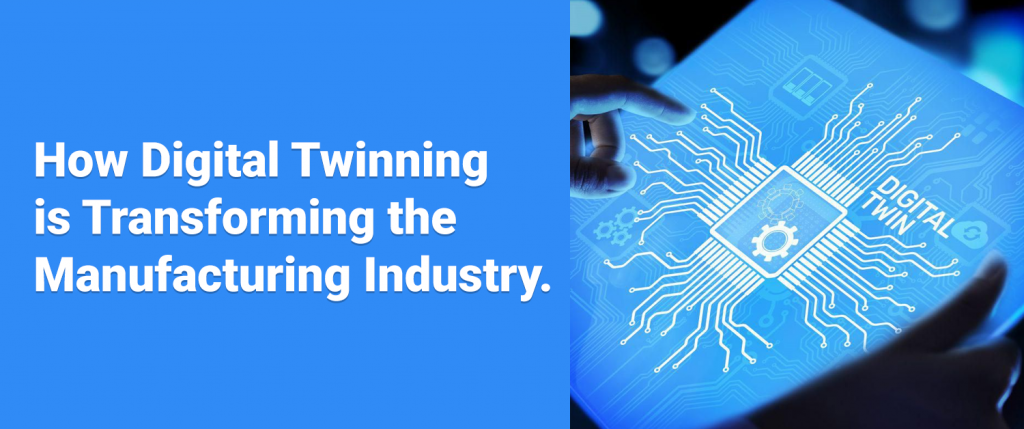
With the rise in digital power, many new technologies are being introduced in the global world. Whether artificial intelligence, machine learning, or even the Internet of Things, the global sector is benefitting a lot from all the disruptive technologies. A digital twins is also one such robust technology that has paved its way in recent times.
Digital twins are a revolutionary technology that has drastically transformed the manufacturing sector. With its ability to reduce the operational costs, and increase the lifespan of the products, digital twinning technology has made it possible for the manufacturing industry to step into Industry 4.0. According to McKinsey, the total value of the industries leveraging digital twins and other IoT applications will be around $11.1 trillion by 2025!
While the number above highlights the growing trend of digital twin technology, many industries are still skeptical about its implementation and benefits. In today’s article, we will be covering everything about digital twin technology; it’s benefits, application, and its future. But first things first!
What is Digital Twin?
Before exploring much about digital twins and its impact in the manufacturing sector, it is first vital to understand the underlying term, i.e., digital twin technology. The term digital twin is nothing but a conceptual term of developing a physical match of any operation or product using data from smart sensors. In other simpler words, it is mapping of physical products with their digital ones, so that they can be used seamlessly on different platforms.
Many times, it is seen that manufacturers had to struggle a lot whenever there is even the slightest change in their production cycle. That change may be due to evolving technology, or revised consumer needs. However, with digital twin technology, that issue could be resolved seamlessly.
Digital twin allows the manufacturers to streamline their operations with the use of smart machines. These intelligent machines learn during their lifetime and simulate future advancements in product development and other activities.
You can seamlessly detect the faults in your machines and operations even before they occur. That makes it easy for you to resolve issues and other vital parts from a third party to repair your machines.
Lastly, not to mention, earlier, the designers had no privileges to test their product completely to detect the faults. However, with the rise in the use of digital twin technology, that thing also resolved to a greater extent. Digital twins provided virtual technology to the designers to test the product to its fullest to detect all the issues and test their effectiveness. That made the final development much quicker, effective, and more useful for the customers. Plus, it also reduced the overall cost of the product!
How Digital Twins Helps Manufacturers to Win the Consumer Demands?
We all know that the Industry 4.0 model relies much on valid data and automation techniques. Digital twin technology creates a perfect environment for you to collect data from every touchpoint and gather them for analytics and simulation. Once the data is analyzed and various tests are run on it, you can use it to frame future strategies and make informed decisions.
Here are some more benefits of the digital twin in enhancing the manufacturing industry!
1. Enhanced Plant Performance
The foremost benefit of the digital twin has enhanced plant performance. The adoption of digital twin technology allows the manufacturers to collect data from shop floors, and that’s the key to automation. The smart sensors and embedded machines integrated into the shop floors provide various vital data to the manufacturer.
Once all the data from equipment, manufacturing processes, and the system is combined with a centralized location, you can run tests to determine your efficiency. In other words, digital twin enables you to create a virtual environment of your shop floor to assess the impact of your policies and change in operations. You can know how your services could be improved and how certain things can be achieved effectively and quickly using a digital twin.
2. Predictive maintenance
Predictive maintenance involves servicing the faulty components at the right time. The digital twin technology, along with AI, and machine learning provides complete information over any element to mitigate system failure.
An excellent example of such an aspect is Mitsubishi Hitachi Power Plant. This digital twin model has been specifically designed for the power plants to monitor the sensors and other vital components of the plant. Once implemented successfully, this digital twin system monitors and reveals all the faulty parts and provides the best time to service them. The system also works with AI, ML, and other disruptive technologies to reduce the plant’s downtime and eliminate resource wastage during the maintenance process.
3. Simplification of Complex Processes
Another critical area, where digital twins have proved an excellent option for the manufacturers is simplifying the complex manufacturing operations. Digital twin, along with AI, has the potential to virtually create the working environment and detect all the issues and challenges that might come in the future. That allows the manufacturers to take actions well in advance, mitigating the losses and controlling the operations.
With digital twin technology, you can even get a proper map of your business operations. You can match your operations’ effectiveness with the set standards and understand deviations and the list of preventive actions that you can take to improve those errors. An example of such a benefit is the National Energy Technology Laboratory of the USA. They deployed digital twin solutions to check the feasibility of carbon dioxide in powering the plants rather than hazardous coal-powered plants.
The technology helped them provide a virtual map for their research and optimized their resources for a better, controlled, and profitable process.
4. Cost and Resource Optimization
As discussed earlier, the use of digital twins not only allows you to see farther aspects of the operation but also helps you in optimizing the resources of your manufacturing operations. The digital twin technology, along with IoT, can test the real-time changes in the object directly on a virtual prototype.
That has not only made the product development and research a piece of cake but has also facilitated automated manufacturing in the global sector. The use of digital twinning has made it seamlessly for the industries to develop an error-free and completely customized product without much difficulty. They can get a holistic approach for their asset management. Furthermore, they can even plan to develop new and different products quickly to satisfy the ever-growing customer needs.
5. Easy Training and Onboarding
The last, but surely not the least benefit of digital twin technology is easy onboarding and training process. We all know that Industry 4.0 is dependent on the use of automated technologies like IoT, Industrial IoT, AI, and automated vehicles. Now, to use such kinds of techniques, your staff should also be well-trained and versed in such things.
Once again, that problem is solved by a digital twin. The robust digital twinning provides a virtual environment for your staff to learn various things without affecting the actual product and operation cycle. That not only results in a cheaper training but also helps them control and analyze the process more quickly and effectively. They can get an idea of optimizing the resources as per the need and how to make the processes more reliable.
Rise of Digital Twin in the Manufacturing Sector
The rise of digital twinning in manufacturing is not a new concept. Many leading firms have already started to leverage digital twins to gain massive profits and brand value. Here are a few ways in which digital twinning is disrupting the manufacturing for the better.
1. Engineering and Designing
Engineering has a long history of leveraging digital twins to enhance its product development phase. The use of digital twinning has been long used in engineering to make it possible for its designers to detect changes and issues prevailing in their product. Digital twin technology provides a virtual prototype of the product, even before it is created.
That can help you to identify how your actual product will look like and what would be its performance after specific features are involved in it!
The same data received from the digital twin and smart sensors could also be applied to enhance the product development process and to make your business ready for future digital waves.
2. Customized Products
Another crucial aspect by which a digital twin impacts the existing manufacturing business is by enabling them to build more customized products. With digital twinning, you can seamlessly incorporate all your customer inputs into your manufacturing processes to make a fully customized product as per their expectations. Let us understand this concept with a simple example.
For instance, your company produces custom cars. The customers can choose the color, variant, and other specifications of the product to fit their use. Now, with traditional designing methods, that process could be a bit tedious. However, the case is a bit different from digital twinning. The digital twin technology will enable you to include all the customizations into the virtual product to test its feasibility.
Once you know how a specific change will impact your product, you can seamlessly plan and offer different variants to your customers at a much lower time. That will not only increase your user engagement but will also enhance your customer services and brand value!
3. Smart Production
Smart machines are no longer a sci-fi thing; instead, they have become an essential future in the manufacturing sector. With the use of intelligent sensors and embedded systems, the growth of digital twins increased tremendously. Today, almost all the leading manufacturing firms are leveraging digital twinning to know the exact faults and issues in their products in real-time.
The digital twinning enables the factories to become smart by providing the exact information on product quality and performance during the complete development life cycle. They can identify the flaws in their current strategies and develop them quicker and at cheaper rates without comprising the qualities.
Besides that, digital twinning even provides all the possible machines breakdown chances to mitigate any severe losses and to enhance the overall productivity of your business operations.
4. Digital Twin in Manufacturing and Beyond
As evident from the points mentioned above, there is no denying that digital twin technology has transformed the manufacturing sector. From predictive maintenance to virtual testing and product prototyping, the digital twin has made it seamless for the manufacturers to develop products and provide them quickly to the clients at a much lesser cost.
However, the scope of digital twins does not remain in the manufacturing industry. Yes, you heard it right! The applications of digital twins have expanded beyond manufacturing, and today, most healthcare institutes are also leveraging digital twinning to enhance their training and operations. For instance, the manufacturers can now learn their operation techniques on the digital twin rather than on the actual patient.
Furthermore, the small sensors, probably the size of the band-aid, can send various health alerts to the doctors to help them analyze any threat or abnormalities related to the patient. The energy sector, the construction sector, and the research sector are also some of the leading industries benefiting from the digital twin technology.
How to use a digital twin to change your manufacturing operations?
All in all, we saw that the digital twin is no less than a boon for most of the leading industries of the global sector, especially for the manufacturing industry. From optimizing the resources to a reduction in downtime and flexible training, robust technology has a lot to offer the existing sectors.
Now, a major question that might be in your mind is, how can we implement digital twins in our existing manufacturing processes? How can we benefit from the robust digital twin technology? Well, here’s the answer to it!
1. Explore Opportunities
The first thing you can do to incorporate a digital twin in your existing operations is to explore the perfect opportunity. You need to identify the critical areas of your manufacturing unit, ready to reap the digital twinning benefits. Any crucial equipment that plays a significant role in your operations or any product that may have many development issues can be your perfect choice.
Remember, digital twinning is a new process for you, and you may have to spend extra money on it. So, carefully choose your units and then implement digital twin technology to witness profound results.
2. Detect the Processes
The next crucial step is to identify the pilot for the digital twin process. Now, here you should always pay heed to the most promising pilot aspect rather than a complex one. It is often seen that companies consider the complex process for the digital twin pilot and, as a result, face challenges afterward.
You should always try to include the most promising process or equipment as a pilot test to reasonably identify the pros and cons of the technology. For that, it is advisable to leverage your change management and operation management system of your organization.
3. Go Slow
Another leading factor that can impact the growth of the digital twin in your manufacturing unit is your excitement. It is often seen that small companies or start-ups after witnessing benefits of the technology, plan to deploy across the whole industry. Now, it is not entirely wrong, but as a start-up, you should at least understand the scope and limitations of the technology that you are implementing in your business.
For that, try to limit the scope of the digital twin in your business operations. Choose a pilot process that is a subset of any significant unit and then witness its growth. If you find the technology to be promising, then you can slowly implement it across your industry. All in all, go broad and witness the promising results of digital twins for your business.
4. Expand Your Pilot
Once your pilot test is successful, you may expand the reach of a digital twin to more areas of your business. For instance, select the areas adjacent to your pilot process. Also, learn from the mistakes and scale it as your business grows.
5. Evaluate your Results
Lastly, you need to evaluate the results after delaying a digital twin in your business operations. Try to make a qualitative and quantitative report based on the results that you got from digital twin processes. You could even monitor the pilot processes or adjourning processes to make an informed decision.
Over to you!
To conclude, we can say that digital twins, a cutting-edge technology, will have promising results for the global industries. With the advancements in artificial intelligence and IoT, the digital twin technology will have more benefits for the manufacturing sector. Even today, the businesses that have deployed digital twin systems are making huge profits in many ways.
For instance, reducing overheads, effective customized products, and agile development are crucial ways digital twin has benefited the manufacturing sector. Further advancements may even result in more complex development, easy testing, and better customizations. All in all, we can surely say that digital twins are one of the promising future of the manufacturing industry. You, as a business, should surely adopt it to reap its amazing benefits.
Are you looking for end-to-end custom IoT solutions for your industry? We have got you covered! We are a leading software engineering firm that can help you enhance your business operations with cutting-edge and latest digital solutions. Contact us anytime, and get a free 30-minute consultation for your project. Till then, Happy Reading!