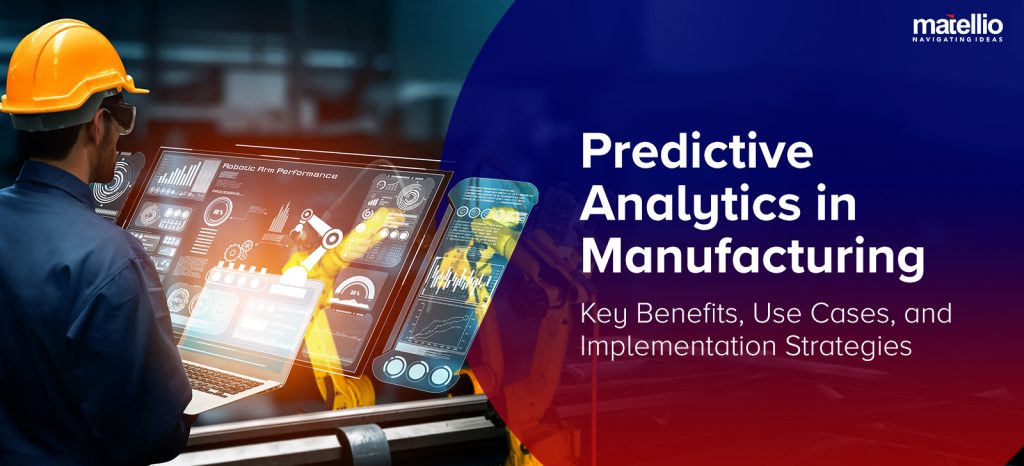
Are unexpected equipment failures causing costly production delays? Are you struggling to maintain consistent product quality and optimize your supply chain? Do high operational costs and a lack of real-time insights hinder your decision-making process? Enter predictive analytics in manufacturing—a powerful solution that can address these issues effectively.
Predictive analytics applications leverage data, statistical algorithms, and machine learning techniques to identify the likelihood of future outcomes based on historical data. Imagine making data-driven decisions that boost efficiency, minimize downtime, and keep your costs in check. Intrigued? Well, that’s what our blog is all about!
This blog dives deep into the transformative power of predictive analytics in the manufacturing industry. We’ll explore its key benefits, real-world predictive analytics use cases in manufacturing, and proven strategies for implementation. Plus, we’ll showcase how Matellio has empowered manufacturers to automate operations and achieve remarkable results through our technology consulting expertise and custom enterprise software development services.
What is Predictive Analytics for Manufacturing, and Why Do You Need It?
As a decision-maker in the manufacturing industry, you are constantly faced with challenges that demand effective solutions. Predictive analytics in manufacturing can be the game-changer you need to overcome these challenges and propel your business to new heights. But what exactly is predictive analytics, and why should you invest in it? Let’s break it down.
Understanding Predictive Analytics
Predictive analytics is a branch of advanced analytics that uses historical data, machine learning algorithms, and statistical techniques to predict future outcomes. By analyzing patterns and trends in your data, predictive analytics services can forecast what is likely to happen next. This proactive approach allows you to make informed decisions, optimize processes, and prevent issues before they occur.
Read More: Unlock the power of predictive analytics in healthcare to enhance patient care, optimize resources, and drive better outcomes.
But why exactly do you need predictive analytics in manufacturing? Let’s explore the best benefits you can enjoy with this manufacturing technology trend:
Minimize Downtime and Maintenance Costs
Imagine knowing exactly when a critical piece of equipment is likely to fail and being able to schedule maintenance just in time to prevent a breakdown. Predictive analytics in the manufacturing industry can provide this foresight. By analyzing data from sensors and maintenance logs, predictive analytics applications can identify signs of wear and tear, allowing you to perform maintenance proactively. This minimizes unexpected downtime and reduces the cost of emergency repairs.
Improve Product Quality
Consistent product quality is crucial for maintaining customer satisfaction and meeting industry standards. Predictive analytics helps you achieve this by analyzing data from various stages of the production process to detect potential quality issues. By addressing these issues in real time, you can ensure that your products consistently meet the highest quality standards, reducing defects and recalls.
Optimize Supply Chain Management
Effective supply chain management is essential for meeting demand, reducing costs, and ensuring timely delivery. Predictive analytics applications and RPA in manufacturing can enhance your supply chain operations by forecasting demand more accurately. This allows you to optimize inventory levels, streamline production schedules, and improve supplier performance. As a result, you can reduce stockouts, minimize excess inventory, and respond more effectively to market changes.
Enhance Operational Efficiency
Operational efficiency is key to staying competitive in the manufacturing industry. Predictive analytics in manufacturing provides insights that help you identify bottlenecks, streamline processes, and make data-driven decisions. By optimizing your operations, you can increase productivity, reduce waste, and make better use of your resources.
Increase Customer Satisfaction
Understanding your customers’ needs and preferences is vital for delivering products that meet their expectations. Predictive analytics use cases in manufacturing can analyze customer data to identify trends and anticipate demand. This allows you to tailor your products and services to meet market needs, improving customer satisfaction and loyalty.
Why Now is the Time to Invest in Predictive Analytics Services – Market Scenario
As per a trusted source, the global market for predictive analytics is projected to grow at a compound annual growth rate (CAGR) of 24.1% from 2023 to 2030. And that’s not all!
Clearly, the manufacturing industry is becoming increasingly competitive, and staying ahead requires leveraging the latest technologies. Investing in predictive analytics in the manufacturing industry now will not only give you a competitive edge but also position your company for long-term success. Here’s why you should consider making this investment:
Data is More Accessible Than Ever
With the rise of IoT development services and smart manufacturing, you have access to more data than ever before. This data is a goldmine of insights waiting to be uncovered by predictive analytics applications.
Advanced Technologies are Readily Available
The tools and technologies needed for predictive analytics in manufacturing, such as machine learning algorithms and cloud computing, are now more accessible and affordable.
Proven Success in the Industry
Many leading manufacturing companies have already successfully implemented predictive analytics in the manufacturing industry and are reaping the benefits. By following their lead, you can achieve similar results.
Reduced Downtime and Maintenance Costs
Unexpected equipment failures can lead to significant production delays and high maintenance costs. Predictive analytics in manufacturing can help you anticipate equipment failures before they occur by analyzing sensor data and historical maintenance records. By scheduling maintenance activities proactively, you can minimize downtime, extend the lifespan of your equipment, and reduce maintenance costs using predictive analytics applications.
Need to Know How Much Will It Cost to Implement Predictive Analytics in Manufacturing?
Common Challenges in Manufacturing
Manufacturing companies face numerous challenges that can impact their efficiency, profitability, and competitiveness. Here are some of the most common challenges:
Equipment Failure and Unexpected Downtime
Unexpected equipment failures can cause significant production delays and lead to increased maintenance costs. These disruptions negatively impact the overall efficiency of the manufacturing process and result in missed deadlines and customer dissatisfaction. Predictive analytics in manufacturing can help address this by forecasting potential equipment failures, allowing proactive maintenance scheduling to minimize downtime and costs.
Quality Control Issues
Maintaining consistent product quality is a major challenge for manufacturers. Variations in raw materials, production processes, and environmental conditions can lead to quality issues that affect the final product. Quality control issues can result in costly recalls, rework, and damage to the company’s reputation. Leveraging predictive analytics applications along with AI integration services can help detect early signs of quality issues, ensuring better quality control.
Supply Chain Disruptions
Supply chain disruptions, such as delays in raw material deliveries, transportation issues, and supplier performance problems, can impact production schedules and increase operational costs. By using predictive analytics in manufacturing, companies can anticipate these disruptions and optimize supply chain management to ensure timely deliveries and reduce risks.
High Operational Costs
Manufacturing processes involve significant costs related to labor, materials, energy, and equipment maintenance. Inefficient processes and resource wastage can further increase operational costs, affecting overall profitability. Predictive analytics use cases in manufacturing show that data-driven insights can optimize operations, reduce waste, and ultimately lower operational costs.
Lack of Real-Time Insights
Real-time data is crucial for manufacturers to make informed decisions and respond quickly to changing conditions. However, many manufacturers struggle with integrating and analyzing data from various sources, leading to a lack of real-time insights. Predictive analytics in the manufacturing industry can help solve this by providing actionable insights from real-time data, improving decision-making and operational efficiency.
Inaccurate Production Planning and Scheduling
Efficient production planning and scheduling are critical for maximizing output and minimizing costs. However, fluctuating demand, equipment availability, and workforce constraints can make it challenging to create optimal production schedules. Inaccurate planning can lead to overproduction, underproduction, and increased lead times. Predictive analytics applications can improve production planning by forecasting demand and optimizing schedules to meet production targets.
Improper Energy Management and Sustainability
Managing energy consumption and minimizing environmental impact are significant challenges for manufacturers. Energy costs are a substantial part of operational expenses, and inefficient energy use can lead to higher costs and increased carbon footprints. By utilizing data analytics in manufacturing, companies can monitor energy usage, identify inefficiencies, and implement sustainable practices to reduce costs and environmental impact.
Predictive Analytics Applications in Manufacturing
Predictive analytics can be applied to various aspects of manufacturing to address challenges and enhance overall efficiency. Here are some key predictive analytics use cases in manufacturing:
Predictive Maintenance
Predictive maintenance uses data from sensors and equipment to predict when maintenance activities should be performed. By analyzing historical maintenance data and real-time sensor data, you can identify patterns that indicate potential equipment failures. This allows you to schedule maintenance activities proactively, reducing unexpected downtime and extending the lifespan of your equipment.
How it benefits your company:
- Minimize unexpected downtime
- Reduce emergency maintenance costs
- Extend equipment lifespan
- Improve operational efficiency
Quality Assurance
Another predictive analytics use case in manufacturing is quality assurance. Predictive analytics can monitor production processes and detect potential quality issues in real-time. By analyzing data from various stages of production, you can identify patterns that may lead to defects and take corrective actions before issues impact the final product.
How it benefits your company:
- Ensure consistent product quality
- Reduce rework and scrap rates
- Prevent costly recalls
- Increase customer satisfaction
Inventory Management
Effective inventory management is crucial for minimizing carrying costs and ensuring timely delivery of products. Predictive analytics in manufacturing can help you forecast demand more accurately and optimize inventory levels. By analyzing historical sales data and market trends, you can predict future demand and adjust inventory levels accordingly, reducing stockouts and excess inventory.
How it benefits your company:
- Optimize inventory levels
- Reduce stockouts and excess inventory
- Lower carrying costs
- Improve supply chain efficiency
Also Read: How Inventory Management Software Development Can Help Overcome Business Challenges
Demand Forecasting
Analytics in manufacturing can improve demand forecasting accuracy by analyzing historical sales data, market trends, and external factors such as economic conditions and seasonal variations. Accurate demand forecasting helps you plan production schedules, manage inventory levels, and optimize your supply chain, leading to increased efficiency and reduced costs.
How it benefits your company:
- Improve production planning
- Reduce lead times
- Avoid overproduction and underproduction
- Enhance customer satisfaction
Energy Management
Energy costs are a significant component of manufacturing expenses. Predictive analytics in manufacturing can help you optimize energy consumption by analyzing data from various energy sources and identifying inefficiencies. By implementing energy-saving measures based on these insights, you can reduce energy costs and improve sustainability.
How it benefits your company:
- Optimize energy consumption
- Lower energy costs
- Reduce carbon footprint
- Achieve sustainability goals
Also Read: Industrial Energy Management Software Development: Fueling Efficiency and Sustainability
Sustainability and Cost Management
Predictive analytics applications can analyze historical energy usage patterns, monitor real-time consumption data, and evaluate energy-saving measures to forecast future energy needs. This enables manufacturers to implement dynamic energy management strategies, optimize consumption, and reduce costs.
How it benefits your company:
- Implement dynamic energy strategies
- Increase energy efficiency
- Reduce operational costs
- Support environmental sustainability
How Matellio Helped a Manufacturing Company to Automate Its Operations and Take a Step Closer to Industry 4.0.
Matellio is a leading consultancy based in the US that specializes in digital transformation services. With extensive experience in the manufacturing sector, we understand the unique challenges faced by manufacturers and offer tailored solutions to drive efficiency and innovation.
The Challenge
Hypertherm was grappling with inefficiencies in reviewing and analyzing performance data stored in their Hypertherm cartridges. Extracting valuable data, such as starts, transfers, and arc-on time, was a time-consuming and cumbersome process. They needed a streamlined solution to simplify data retrieval and analysis, allowing them to identify areas for improvement and opportunities for operator training.
The Solution
Recognizing the need for an innovative solution, Matellio partnered with Hypertherm to develop the Hypertherm Cartridge Reader App. This mobile application revolutionized their data management process by enabling users to scan cartridges using an NFC reader and view detailed data directly on their mobile devices.
Key Features of the Hypertherm Cartridge Reader App
Profile Setup and Custom Experience
Users can set up profiles and choose their preferred experience, including estimating cartridge life expectancy based on arc hours or successful transfers. This customization ensures that users receive relevant and actionable insights tailored to their needs.
Job Compatibility Analysis
The app provides a job compatibility analysis based on user inputs and scanned data, helping users determine the best cartridge for their specific tasks. This feature enhances operational efficiency by ensuring optimal cartridge usage.
Unconnected Experience
For users without an antenna, the app offers an unconnected experience that includes links to instructional videos and access to manuals. This ensures that all users, regardless of their equipment, can benefit from the app’s features.
Data Synchronization
The setup process collects company and job information, syncing it with scanned cartridge data on Microsoft Azure Data Lake. This integration enhances data functionality and allows for comprehensive data analysis.
Benefits Achieved Through This Collaboration
The Hypertherm Cartridge Reader App, developed by Matellio, has empowered Hypertherm and its users with numerous benefits, including:
Seamless Cartridge Management
The app provides a user-friendly and informative platform for efficient cartridge management, reducing the time and effort required to extract and analyze data.
Informed Decision-Making
Users are equipped with detailed cartridge data, such as end-of-life indicators and usage information, enabling them to make informed decisions and optimize their operations.
Enhanced User Engagement
Integrated tutorial videos within the app enhance user engagement and understanding, making it easier for operators to utilize the app effectively.
Comprehensive Features
Features like job compatibility analysis and recycling program promotion improve usability and overall efficiency, ensuring that users get the most out of their Hypertherm cartridges.
Result
Our collaboration with Hypertherm showcases Matellio’s expertise in developing customized solutions for manufacturing companies. By automating their data retrieval and analysis process, we helped Hypertherm overcome significant challenges and achieve greater efficiency in their operations.
If you’re looking to automate your manufacturing operations and leverage data for better decision-making, Matellio has the experience and solutions you need to succeed.
Want to Witness a Similar Digital Transformation for Your Manufacturing Company?
Implementation Strategies for Predictive Analytics
Successfully implementing predictive analytics in manufacturing requires a strategic approach. For instance, you need to have knowledge of various tools and technologies to achieve desirable results with analytics in manufacturing. Moreover, you need to have a talented team of experts who can guide you throughout the implementation process.
That’s where Matellio steps in—your trusted manufacturing technology consulting partner.
At Matellio, we have extensive experience collaborating with manufacturing companies like yours. Our proven track record in custom manufacturing software development, combined with a deep understanding of predictive analytics in the manufacturing industry, can be a valuable asset for your company. Here’s how you can implement analytics in manufacturing by partnering with our experts:
Identifying High-Impact Opportunities:
Our first step is to collaboratively pinpoint the areas where predictive analytics can deliver the most significant impact for your business. This could involve:
- Predictive Maintenance: Anticipate equipment failures before they occur, minimizing downtime and maintenance costs.
- Quality Control: Identify potential quality issues early in the production process, reducing scrap and rework.
- Inventory Management: Optimize inventory levels to avoid stockouts or overstocking, ensuring smooth production flow.
- Demand Forecasting: Gain insights into future customer demand patterns, allowing for better production planning and resource allocation.
You can easily schedule a free 30-minute consultation call with us to discuss your pain points or requirements.
Data: The Foundation of Success
Predictive analytics in manufacturing thrives on data. Once your pain points are clear, we’ll work together to collect data from various sources, including:
- Machine Sensors: Real-time data on equipment performance, vibration, temperature, etc.
- Production Systems: Production logs, machine settings, and output data.
- Historical Records: Past maintenance records, quality control data, and sales history.
The key is to ensure data accuracy, completeness, and accessibility. We’ll help you integrate data from various sources to create a unified and robust dataset for analysis.
Choosing the Right Tools and Technologies
Selecting the most suitable predictive analytics applications and tools is crucial. Here at Matellio, we have extensive experience working with various platforms and can recommend the best fit for your needs. Some factors to consider include:
- Machine Learning Algorithms: Adopt machine learning services to leverage techniques like anomaly detection and regression analysis to identify patterns and predict future outcomes.
- Statistical Modeling: Tools to analyze historical data and identify relationships between variables.
- Data Visualization Tools: Interactive dashboards to effectively communicate insights and trends to stakeholders.
- Scalability: Consider your future growth plans and ensure the chosen technology can accommodate your data volumes.
- Ease of Use: Selecting tools with user-friendly interfaces for your team to leverage effectively.
- Compatibility: Ensuring seamless integration with your existing manufacturing systems and software infrastructure.
Building a Data-Driven Culture
Successful implementation of predictive analytics in the manufacturing industry goes beyond just technology consulting services. As your technology partner, we’ll collaborate with you to develop a data-driven culture within your organization. This includes:
- Training Programs: Equipping your staff with the knowledge and skills to understand the value of data and utilize predictive analytics tools effectively.
- Communication & Collaboration: Fostering a culture of open communication and collaboration between operational teams and data analysts.
- Data-Driven Decision Making: Encouraging decision-making based on insights gleaned from predictive analytics rather than intuition or guesswork.
Continuous Improvement and Monitoring:
Predictive analytics applications are an ongoing journey, not a one-time fix. We’ll partner with you to continuously monitor the performance of your models and refine them as needed. Regular adjustments ensure your models remain accurate and reflect any changes in your manufacturing processes or market conditions.
Let’s Start the Implementation of Predictive Analytics in Manufacturing with a Free 30-minute Consultation!
Conclusion
To conclude, we can say that predictive analytics offers a powerful solution to the common challenges faced by manufacturing companies. By leveraging data, statistical algorithms, and machine learning techniques, you can enhance operational efficiency, reduce downtime, improve product quality, optimize supply chain management, and increase customer satisfaction.
As a decision-maker, adopting predictive analytics in manufacturing is no longer an option for you but a necessity to stay competitive in the market. Matellio, with its expertise in digital transformation services, custom manufacturing software development, and data consulting services, can assist you in your journey toward predictive analytics implementation.
Contact us today to learn how we can help you harness the power of predictive analytics and drive your manufacturing operations to new heights. Let us be your partner in achieving operational excellence and business success.
FAQs
Q1. What is predictive analytics in manufacturing operations?
Predictive analytics in manufacturing operations involves using historical data, statistical algorithms, and machine learning techniques to predict future outcomes and trends. By analyzing data from sensors, production logs, and various other sources, predictive analytics helps manufacturers anticipate equipment failures, optimize maintenance schedules, improve product quality, manage inventory, and streamline supply chain operations.
Q2. Which businesses can use predictive analytics services?
Predictive analytics services are beneficial for a wide range of businesses within the manufacturing sector. This includes, but is not limited to, automotive manufacturers, electronics producers, metal fabricators, pharmaceutical companies, food and beverage processors, and aerospace industries. Any manufacturing business that relies on complex machinery, quality control, and supply chain management can leverage predictive analytics to enhance operational efficiency, minimize downtime, and improve product quality.
Q3. What is a common predictive analytics application?
A common predictive analytics application in manufacturing is predictive maintenance. This application involves analyzing data from equipment sensors and maintenance logs to predict when machinery is likely to fail. By identifying signs of wear and tear early, manufacturers can schedule maintenance activities proactively, reducing unexpected downtime and minimizing maintenance costs. Predictive maintenance ensures that equipment operates efficiently, extending its lifespan and improving overall productivity.
Q4. What will the cost of implementing predictive analytics in manufacturing be?
The cost of implementing predictive analytics in manufacturing can vary widely based on several factors, including the complexity of the manufacturing processes, the amount and type of data to be analyzed, the specific predictive analytics tools and technologies used, and the level of customization required. It's better to discuss your pain points and requirements with a consultancy to get an exact cost of implementation. You can fill out our form to book a free 30-minute consultation for your project!
Q5. How can I get started with Matellio for my project?
Getting started with Matellio for your predictive analytics project is straightforward. Follow these steps:
- Fill out our form with your basic details and a message to get in touch with our experts.
- Discuss your needs and pain points with our experts over a free 30-minute call.
- Based on the assessment, Matellio will provide a customized proposal outlining the proposed solution, implementation timeline, and cost estimates.
- Once the proposal is approved, we'll develop a detailed implementation plan, including data collection and integration, tool selection, and staff training.
- Matellio will execute the implementation plan, continuously monitor the performance of predictive models, and provide ongoing support to ensure your project's success.